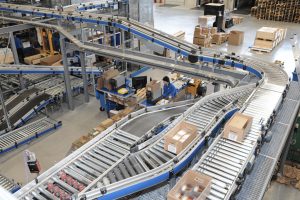
Hilpotstein. Kernstück des Zentrallager von Keller & Kalmbach hierbei ist die Kommissionierung. Neben der Effizienz der Prozesse war die ergonomische Gestaltung der Kommissionier-Arbeitsplätze einer der wichtigsten Anforderungen an den Generalunternehmer Jungheinrich.
Wenn man die A9 von München nach Nürnberg fährt, dann gibt es eine Menge zu sehen. Und auf der Höhe von Hilpoltstein wird es dann richtig interessant. Hier überragt ein blendend weißer Komplex alles in der Nähe befindliche. In großen Lettern prangt ein Schriftzug an der Fassade: Keller & Kalmbach.
Das Unternehmen wurde 1878 in München als Großhandel für Schrauben und Schmiedebedarf gegründet. Heute gehört Keller & Kalmbach zu den führenden Großhandelsbetrieben unter anderem für Verbindungselemente, Schrauben, Befestigungstechnik und Dübel sowie Zeichnungsteile, Handwerkzeuge, Elektrowerkzeuge und Hebezeuge. Hinzu kommen Erzeugnisse in den Bereichen Arbeitsschutz und Betriebseinrichtungen sowie Chemisch-Technische Produkte.
„Eine Erweiterungs- und Rationalisierungsinvestition“
Das Unternehmen hat seinen Sitz in Unterschleißheim bei München. Keller & Kalmbach beschäftigte seinerzeit etwa 450 Mitarbeiter und hatte dabei einen Jahresumsatz von mehr als 150 Millionen Euro. Die über 20.000 Kunden des Unternehmens kommen aus den Bereichen Automotive, Industrie und Handwerk. Keller & Kalmbach verfügt deutschlandweit über mehr als zwei Dutzend Standorte.
„Jüngster Meilenstein unseres Unternehmens war die Errichtung und Inbetriebnahme eines neuen Zentrallagers für den C-Teile-Großhandel in Hilpoltstein südlich von Nürnberg“, erzählt Dr. Ingomar Schubert, Leiter Supply Chain Management bei Keller & Kalmbach. Nach etwa eineinhalb Jahren Bauzeit erfolgte Mitte 2009 die Inbetriebnahme in eben jenem weißen Komplex direkt an der Autobahn. Schubert spricht in Zusammenhang mit der Errichtung des neuen Zentrallagers sowohl von einer Erweiterungs- als auch einer Rationalisierungsinvestition.
Das vorherige Zentrallager in Unterschleißheim bei München entsprach mit seinen 9.000 Palettenstellplätzen und etwa 60.000 Stellplätzen für Kleinteilebehälter bereits seit längerem nicht mehr den Anforderungen von Keller & Kalmbach. Da eine Erweiterung am Standort Unterschleißheim nicht möglich war, fingen insgesamt neun kleinere, im süddeutschen Raum befindliche Filiallager zunächst die immer steigenden Lagerkapazitäten auf.
„Um dem Wachstum von Keller & Kalmbach sowohl qualitativ als auch quantitativ gerecht zu werden, war es unumgänglich, ein neues, modernes Distributionszentrum zu errichten“, sagt Schubert. Hierfür hatte Jungheinrich als Planer und Generalunternehmer den Auftrag erhalten. „Wichtig bei der Vergabe war vor allem der Punkt, dass Jungheinrich alles aus einer Hand geboten hat!“, so Schubert weiter. Für Keller & Kalmbach sei außerdem der Kundendienst besonders wichtig gewesen: „Auch unser Geschäft würde ohne einen professionellen Kundendienst so nicht laufen!“
Vier Lagerbereiche
Zum neuen Distributionszentrum zählen vier Lagerbereiche: ein automatisches Palettenhochregallager als Kommissionierlager für große Auftragspositionen sowie als Nachschublager, ein automatisches Kartonlager für kleine Positionen und als Kommissionierlager, ein automatisches Tablarlager als Leergutlager für KanBan-Behälter sowie ein Lager für sperrige Güter. Die Steuerung aller Lagerbereiche sowie des hoch komplexen Kommisionierbereiches erfolgt durch die Lagerverwaltungssoftware Jungheinrich WMS.
Durch eine entsprechende Anordnung der Lagerbereiche ist Keller & Kalmbach in der Lage, auf zukünftige Entwicklungen zu reagieren, und Lagerbereiche gegebenenfalls auch auszubauen. Dr. Ingomar Schubert: „Dies ermöglicht uns tatsächlich die flexible Nutzung unseres neuen Zentrallagers für eine sehr, sehr lange Zeit – auch bei Veränderungen des Geschäftes.“
Hauptaugenmerk: Auswahl des Kommissioniersystems
Um eine hohe Effizienz in der Kommissionierung zu erreichen, wurde bei der Konzeption des Distributionszentrums ein Hauptaugenmerk auf die Gestaltung des Kommissioniersystems gelegt. Den Kommissionierbereich konzipierte man nach dem Prinzip „Ware zum Mann“. An jedem der zehn Kommissionier-Arbeitsplätze kann von verschiedenen Bereitstelleinheiten kommissioniert werden. Die entsprechende Fördertechnik aus dem Paletten- sowie beiden Kleinteilelagern verläuft auf mehreren Ebenen.
„Durch dieses auf mehreren Ebenen realisierte System besitzt Keller & Kalmbach die gewünschte hohe Flexibilität hinsichtlich der Arbeitsweisen an den Kommissionierplätzen“, erläutert Dr. Stefan Seemüller, Leiter Automatische Systeme im Geschäftsbereich Logistiksysteme bei Jungheinrich.
Sechs Arbeitsweisen: Die hoch flexible Kommissionierung bei Keller & Kalmbach
- Kommissionieren von Lagerpalette auf Versandpalette
- Kommissionieren aus Kleinteilebehälter auf Versandpalette
- Kommissionieren aus Kleinteilebehälter in Versandkarton
- Kommissionieren von Lagerpalette in Versandkarton
- Füllen von KanBan-Behälter mit Ware von der Lagerpalette
- Füllen von KanBan-Behälter mit Ware von Kleinteilebehältern
Prinzip „Ware zum Mann“
„Wir haben uns für eine Kommissionierung nach dem Prinzip ‚Ware zum Mann’ mit manueller Entnahme und dezentraler Abgabe entschieden“, unterstreicht Ingomar Schubert, „bei der nicht nur die Ware, sondern auch zu füllende KanBan-Behälter automatisch bereitgestellt werden.“
Zu den Gründen zählt der Logistikfachmann insbesondere die gleichmäßige Auslastung über das Jahr, die homogene Verteilung auf die verschiedenen Artikel sowie die hohen Artikelgewichte. Die Kommissionier-Arbeitsplätze wurden von Jungheinrich gemäß den Anforderungen so konzipiert und errichtet, dass sie gleichermaßen mit den unterschiedlichsten Bereitstell- und Versandeinheiten versorgt werden können.
Hohe ergonomische Anforderungen
Das ergonomische wie auch das technologische Konzept der insgesamt zehn multifunktionalen Kommissionier-Arbeitsplätze bei Keller & Kalmbach ermöglicht die effiziente Ausführung der verschiedensten Arbeitsweisen bei der Kommissionierung durch die Mitarbeiter. „Die ergonomische Gestaltung der Kommissionier-Arbeitsplätze war eine explizite Kundenanforderung“, erinnert sich Seemüller. So fände beispielsweise das Abschieben nicht mehr benötigter Ladungsträger nur nach vorn und nicht zur Seite statt, um unnötige Drehbewegungen der Kommissionierer zu vermeiden.
Darüber hinaus werden alle Handgriffe auf einer optimierten ergonomischen Höhe ausgeführt. „Das ist insofern wichtig, da auf Grund der hohen Unterschiedlichkeit der zu kommissionierenden Artikel hier nur eine manuelle Entnahme möglich ist“, ergänzt Schubert. Um bei Keller & Kalmbach letzte Zweifel hinsichtlich der Erfüllung der hohen ergonomischen Anforderungen auszuräumen, wurde während der Planungsphase ein Kommissionierplatz beispielhaft am Jungheinrich-Standort Moosburg aufgebaut und mit dem Kunden diskutiert.
Obgleich das ausgeschöpfte Rationalisierungspotenzial an den kombinierten Kommissionierplätzen bereits erheblich war, reichte dies für Keller & Kalmbach. noch nicht aus.
Schubert: „Kommissioniert der Mitarbeiter nun zusätzlich gleich in den Versandbehälter, hat das zum Vorteil, dass die Ware im gesamten Prozess nur noch zwei Mal angefasst werden muss – und zwar am Wareneingang und eben bei der Kommissionierung. Dadurch haben wir weiteres erhebliches Rationalisierungspotential realisieren können!“
Stärken des Kommissioniersystems
Kommissionieraufträge werden bei Keller & Kalmbach stets zu einer Sendung zusammengefasst. Hierzu fasst das Jungheinrich WMS die vom HOST-System kommenden Kundenaufträge nach bestimmten Kriterien – beispielsweise der Lieferadresse – zusammen und bildet Sendungen. „So eine Sendung kann theoretisch unendlich viele Kommissionieraufträge enthalten“, erläutert Dr. Markus Heinecker, Leiter Warehouse Management Systeme bei Jungheinrich.
Ein weiteres Highlight des Kommissioniersystems von Jungheinrich sei die Versandartbestimmung, so Heinecker weiter. „Bei Keller & Kalmbach unterscheiden wir mehrere Arten – unter anderem den Palettenversand oder den Versand von Kleinmengen in Kartons.“ Während der Versand von Paletten über eine große Spedition abgewickelt wird, erfolgt der Versand der kartonierten Kleinwaren über einen Paketdienstleister.
Sonderaufträge können effizient gesteuert werden
„Das Jungheinrich WMS erkennt anhand der in den Stammdaten hinterlegten Artikelgewichten das Gesamtgewicht des Kommissionierauftrages und sorgt automatisch für die Bereitstellung der passenden Versandeinheiten – Karton oder Palette“, erläutert Markus Heinecker, „Automatisch werden dann diese Informationen an den passenden Dienstleister gemeldet und somit der Versand entsprechend veranlasst.“
Darüber hinaus verfügt jeder Kommissionierplatz über einen so genannten „Arbeitsplatzstatus“. Heinecker: „Wenn ein Arbeitsplatz ‚aktiv’ ist, dann bedeutet das, dass hier alle Kommissionieraufträge abgearbeitet werden dürfen. Ist der Platz „passiv“, können ihm vom WMS nur bestimmte Aufträge zugeordnet werden, zum Beispiel nur von bestimmten Kunden oder Aufträge mit hoher Priorität.
Mitarbeiter werden eingebunden
„Kommissionierplätze können auch gesperrt werden, wenn beispielsweise nicht alle zehn Plätze benötigt werden. Wir haben diesen jederzeit änderbaren Status in das Kommissioniersystem integriert, damit das Gesamtsystem entsprechend flexibel arbeitet und beispielsweise Sonderaufträge effizient gesteuert werden können“, so Markus Heinecker.
Neben der ergonomischen Gestaltung der Kommissionier-Arbeitsplätze und der hohen Effizienz der Abläufe war Keller & Kalmbach auch wichtig, die Mitarbeiter in Entscheidungen an ihrem Arbeitsplatz mit einzubeziehen. So wurde von Jungheinrich beispielsweise ein so genannter „Kommissionier-Dialog“ aufgebaut, mit dem man alle Aktion durchführen kann.
Flexible Entscheidungswege
Das gilt unter anderem für die Organisation des Nachschubs. Normalerweise wird, sobald die definierte Mindestmenge eines Artikels im Kartonlager unterschritten wird, vom WMS automatisch ein Nachschubauftrag an das Palettenlager gesendet. Eine passende Palette wird ausgelagert und zu einem der Kommissionierplätze gebracht. Dort wird die Ware vereinzelt und kartonweise in das automatische Kleinteilelager eingelagert.
Der Mitarbeiter kann aber auch die Entscheidung zum Nachschub selber treffen. „Das ist meist dann der Fall“, erläutert Heinecker, „wenn die Restmenge auf einer Palette nach der Entnahme so niedrig ist, dass es sich augenscheinlich nicht lohnt, die Ware wieder zurück ins Palettenlager zu fahren.“
Effizienzsteigerung
„Die Kommissionier-Arbeitsplätze bei Keller & Kalmbach ermöglichen ein flexibles und gleichzeitig sehr effizientes Arbeiten“, fasst Dr. Ingomar Schubert zusammen, „da alle Waren, unabhängig davon, in welchen Gebinden sie beim Kommissionierer ankommen, an jedem Platz bereit gestellt werden.“ Auf diese Weise müsse der Kommissionierer nur noch die Tätigkeiten durchführen, die nicht automatisiert werden können.
„Das befreit den Menschen von monotoner Arbeit und trägt zur Effizienz unserer Prozesse aber auch zur Motivation unserer Mitarbeiter bei.“ Letzteres gelte zudem, wenn Mitarbeiter, seien sie von Keller & Kalmbach oder von Jungheinrich, auf der A9 fahren und an der Ausfahrt Hilpoltstein den strahlend weißen Komplex zu Gesicht bekommen.
jak – 2010