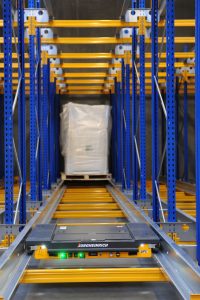
Holstebro. Das Thema Effizienz stand ganz oben bei den Überlegungen, die logistischen Abläufe im Lager von Arla Foods zu optimieren. Ein Kompaktlagersystem mit Unterfahrshuttlen von Jungheinrich sorgt nun dafür, dass am Standort Holstebro nahezu der gesamte zur Verfügung stehende Raum für die Lagerung von Milchproteinpulver effektiv genutzt werden kann.
Als Elo Kristensen das erste Mal auf einem Stapler saß, da war das mit der Bedienung des Fahrzeugs noch so eine Sache. Kein Wunder, Elo war damals zehn Jahre alt, und wusste auch noch nicht, was ihn später einmal beruflich erwarten würde. Heute ist er 47, und lenkt den Elektro-Gegengewichtsstapler von Jungheinrich mit sicherer Hand durch das Lager von Arla im dänischen Holstebro. „Die Paletten müssen bereitgestellt werden!“, ruft er vom Fahrersitz, schmunzelt und fährt sichtlich entspannt an den Besuchern vorbei zum Warenausgang.
Ja, man sitze schon sehr bequem auf diesem Fahrzeug von Jungheinrich, erzählt Elo Kristensen, nach dem der Auftrag abgearbeitet worden ist. Der ergonomisch gestaltete Arbeitsplatz, so heißt es im Typenblatt des EFG 218, mit dem Kristensen durch die Lagerhallen von Arla fährt, gewährleistet ein entspanntes und ermüdungsfreies Arbeiten.
Dass dies nicht nur eine Plattitüde ist, unterstreicht Jens Korbo, Warehouse Manager bei Arla in Holstebro: „Wenn unsere Fahrer sich auf den Staplern nicht nur sicher, sondern auch wohl fühlen, dann spiegelt sich dies eins zu eins in der Effizienz unserer gesamten Abläufe wider!“
Stichwort Effizienz: In dem etwa 10.000 Quadratmeter großen Lager von Arla Foods ampa in Holstebro, etwa 300 Kilometer nordwestlich von Kopenhagen, wird ausschließlich Milchproteinpulver gelagert. Die Herstellung erfolgt in einer wenige Kilometer entfernten Arla-Molkerei. „Das Milchproteinpulver liefern wir in nahezu jeden Winkel dieser Erde“, erzählt Jens Korbo stolz, „mit Ausnahme von Australien, Neuseeland und des afrikanischen Kontinents.“
„Wollten Effizienz am Standort deutlich erhöhen“
Das Milchproteinpulver wurde – abgepackt in kleinen und großen Säcken – bis Mitte 2012 entweder im Blocklager oder in einfachen Einfahrregalen gelagert. Die großen Säcke, die ein Gewicht von 500 Kilogramm auf die Waage bringen, machen etwa 35 Prozent des gesamten Lagers aus.
Dieser Teil wird seitdem in einem Kompaktlagersystem gelagert. „Wir wollten die Effizienz unserer Lagerhaltung hier am Standort deutlich erhöhen, den gesamten uns zur Verfügung stehenden Raum so gut wie möglich nutzen“, so Korbo weiter. Und bei dieser Effizienz-Überlegung kam wiederum Jungheinrich ins Spiel.
Um den zur Verfügung stehenden Platz in der Tat so gut wie möglich auszunutzen, schlug der Intralogistiker mit Sitz in Hamburg Arla vor, das Lager mit einem kompakten Kanallagersystem inklusive der dazugehörigen Shuttle auszurüsten.
„Das Leistungsspektrum eines klassischen Kompaktlagers, also die Platzeinsparung durch den Wegfall von Arbeitsgängen, wird durch die Nutzung von Shuttlesystemen erweitert“, erläutert Lars Baltzer Eriksen, Systemfachmann bei Jungheinrich und Leiter des Projektes bei Arla in Holstebro. „Zusätzliche Optimierungspotentiale, beispielsweise hinsichtlich des Füllgrads, der Umschlagleistung oder des Raumnutzungsgrads, können so problemlos realisiert werden.“
Das Kompaktlagersystem bei Arla wurde so konstruiert, dass jeder Kanal exakt 13 Paletten aufnehmen kann. „Bei zwei Kanälen übereinander entspricht diese genau einer Lkw-Ladung“, erzählt Elo Kristensen, „und Lkw-bezogen lagern wir die Paletten ein oder aus.“
Bei Arla entschied man sich hinsichtlich Wahl des Shuttles für einen Unterfahrshuttle, einen so genannten Under Pallet Carrier (UPC). Der Grund: „Dieser arbeitet besonders effektiv beim wiederholten Ein- und Auslagern im selben Palettengang – wie eben bei Arla“, sagt Eriksen.
Das Jungheinrich-Kompaktlagersystem bei Arla besteht aus dem Carrier (UPC), dem Trägerfahrzeug (EFG 218) und dem Kanalregal selber. Bei der Einlagerung wird der UPC auf die Gabeln des Trägerfahrzeugs aufgenommen und im Palettenkanal eingesetzt. Hier unterfährt der UPC selbständig die Palette und nimmt so die zu transportierende Ware auf seiner Plattform auf, ohne dabei mit dem Trägerfahrzeug physisch verbunden zu sein.
Nach dem Absetzen auf der UPC-Schiene im Regalkanal und dem Drücken der Starttaste auf dem Bedienterminal im Stapler führt der Shuttle die Steuerung alle Fahr- und Hubbewegungen selbständig aus. Sensoren erkennen die Position der eingelagerten Paletten, wodurch eine Ein- bzw. Auslagerung neuer Paletten kollisionsfrei von Statten geht.
Große Effizienzsteigerung
Während einer Fahrt des Shuttles im Kanalgang kann der Fahrer des Trägerfahrzeugs sofort eine weitere einzulagernde Palette holen und am Kanalanfang absetzen. Die nächste Einlagerung wird somit bereits gestartet. Die Auslagerung von Paletten erfolgt analog.
„Seit dem wir den UPC von Jungheinrich nutzen, ist die Arbeit hier viel effizienter!“, sagt Elo Kritensen, schaut zu seinem Chef Jens Korbo, und scheint immer noch über den Effektivitätsschub hier im Lager von Arla zu staunen. Korbo ergänzt: „Ja, die Arbeit hier geht in der Tat schnell von Statten. Zudem bietet uns das gesamte System eine sehr große Flexibilität! Unter dem Strich ist das, was Jungheinrich hier für uns auf die Beine gestellt hat, eine kleine, aber feine Gesamtlösung!“
Zu einer solchen gehörten natürlich auch Flurförderzeuge, ergänzt Lars Baltzer Eriksen. Neben dem EFG 218, der als Trägerfahrzeug für die Under Pallet Carrier dient und die Ware vom Kompaktlager in den Warenausgang schafft, sorgen Elektro-Deichsel-Gabelhubwagen vom Typ ERE 225 für die Be- und Entladung der Lkw sowie den Transport der Ware ins Kompaktlager.
„Diese Fahrzeuge können so ihre Stärken besonders ausspielen“, sagt Eriksen. Hinzu kommt, dass der ERE 225 von Jungheinrich über eine feste Standplattfom verfügt, und somit auf Geschwindigkeiten von über zwölf Kilometern in der Stunde kommt. Eriksen weiter: „Dadurch ist es möglich, dass die Waren besonders wirtschaftlich transportiert werden können.“
Sehr geringer Energieverbrauch
Wirtschaftlichkeit ist auch das Credo bei dem EFG 218. Zum Einsatz kommt bei diesem Fahrzeug die neueste Generation der Jungheinrich-Drehstromtechnik. „Durch den optimalen Wirkungsgrad und die Energierückgewinnung beim Bremsen und Absenken der Last ist der Energieverbrauch sehr, sehr gering“, sagt Lars Baltzer Eriksen. Und Elo Kristensen pflichtet ihm bei: „Egal, wie viel wir fahren, den Stapler brauchen wir nur alle zwei Tage aufladen!“
Und nicht nur die großen Reichweiten der Jungheinrich-Elektrostapler tragen bei Arla Foods in Holstebro zur Effektivitätssteigerung bei. Dazu gehöre auch, dass vor Ort nur ein Servicetechniker benötigt wird, der in der Lage ist, sowohl die Flurförderzeugeflotte als auch die Shuttle zu warten.
Zusammen gefasst kann man sagen: Die Kooperation zwischen beiden Unternehmen läuft völlig problemlos. „Jungheinrich und Arla haben hier in Holstebro viel gemeinsam geschaffen“, so Jens Korbo abschließend. Das Ganze sei eine „richtige win-win-Situation.“ Und Elo Kristensen ergänzt lächelnd: „Wenn ich mit zehn Jahren schon geahnt hätte, welchen Spaß diese Arbeit macht, hätte ich vielleicht so manchen beruflichen Umweg gar nicht erst genommen.“
jak – 2014