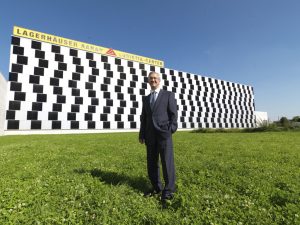
Aarau. Jungheinrich has constructed a new automated high rack warehouse for the logistics service provider Lagerhäuser Aarau AG in Buchs, Switzerland. The special features: Six order picking aisles in the high rack storage area immediately adjacent to the five aisles, redundant conveyor technology assisting reciprocally, if required, and rack servicing cranes that can adapt their operations to the order books.
Lagerhäuser Aarau AG, a company belonging to Lagerhäuser der Centralschweiz AG, is an old-established Swiss company founded in 1873 just as a transport and storage company. They now have their own logistics centres in Spreitenbach, Schafisheim and Hunzenschwil.
Lagerhäuser Aarau AG is specialised on complete logistics solutions for customers in the most varying branches. These include Nestlé, Masterfoods, Cadbury, Gustav Gerig and Blattmann-Cerestar in the food and semi-luxury food sector and in the non-food sector for example General Motors, SIBIR, ABB, Elcotherm, Swatch, Piaggio and Electrolux.
Various Tasks
Apart from transporting and storing goods, Lagerhäuser Aarau AG takes care of a smooth process in additional logistics services. Among these services are stock management and quality control but also order picking and pricing as well as co-packaging.
This includes for example shrinking, bandaging or packaging in special containers and creating displays. Apart from one hundred percent traceability of goods, the company also guarantees a 24 hour service with its own modern vehicle fleet.
Looking Back
To accommodate steadily increasing market requirements, Lagerhäuser Aarau AG already decided earlier to build another high rack warehouse in Hunzenschwil. The location presented itself because of the motorway proximity to the north and the railway connection running parallel in the south.
An automated high rack warehouse was built exactly between both traffic carriers on an area of approximately 10.000 square meters and this is now known virtually throughout the country due to its several times awarded front elevation. Lagerhäuser Aarau AG was searching for a suitable partner for the demanding task of designing, planning and implementing an effectively operating automated high rack warehouse.
High Flexibility and Quick Reaction Time
Invitations to tender for the project were issued to the entire German-speaking region. In the opinion of the client, Jungheinrich was most convincing among more than a dozen potential suppliers. Ulrich Gloor, Head of Logistics and also member of the Board of Lagerhäuser Aarau AG, Schafisheim, recounts: “Apart from the excellent conception, the decisive factor above all was the high flexibility and quick reaction time of Jungheinrich.”
The ability to adapt to the wishes and expectations of Lagerhäuser Aarau AG was very impressive. “During the entire project process, cooperation was at a very high and above all partnership level,“ Gloor continues. “I value this kind of cooperation very much!”
Project Handed Over One Year After the Order Was Placed
After programming all controls, commissioning the warehouse administration system and interfaces to the ERP system, the entire project was handed over to the customer just one year after the order was placed. Lagerhäuser Aarau AG then started to store the first goods and together with this, an automated high rack warehouse of a special kind was commissioned.
It has an integrated order picking level on the ground floor – this means at the second lowest racking level. “Dynamic order picking of goods can be carried out like this – right within high storage racking,” reports Thomas Bürgisser, Head of Logistics Systems at Jungheinrich AG, Switzerland, and responsible for the entire project at Lagerhäuser Aarau AG. 1.000 order picking positions in total are here.
Effective Logistics
The high rack warehouse is 38 metres wide, 110 metres long and 25 metres high. There is capacity for more than 20.000 pallets. The installation is designed for stacking and retrieving 160 pallets per hour. This means 80 pallets each per hour via Goods-in and Goods-out in the south (by rail) and respectively in the north (by lorry).
The effectiveness of the entire logistics is evident when looking at the apron in the north. Fork lift trucks pick up the palleted goods arriving by lorry and deposit them on the apron. The staff then record the products with a hand-held barcode scanner. The barcode data is transferred by radio to the warehouse administration system that controls the internal process, i.e. the entire logistics at Lagerhäuser Aarau AG.
Fully Automated Stacking and Retrieval of Pallets
The products then go from the apron into the high rack storage where they are again identified and checked by the barcode scanner. Faulty goods are removed. One of the two vertical conveyors picks up the pallet and takes it up to a 3.80 metres high structural steel platform. The pallet now reaches the pick-up point of the rack servicing cranes (RGB) in high rack storage via roller conveyors and crosswise moving carriages.
The five rack servicing cranes in the high rack storage of Lagerhäuser Aarau AG are rail guided and move in aisles of 100 metres length between two double-deep racking rows in each aisle. The RGBs work with telescopic forks and can pick up two pallets each. The job of the rack servicing cranes is the fully automated stacking and retrieval of pallets with one tonne load weight each.
Precise Clock Cycle Processes
“Process-safe control of retrieval is, of course, also ensured,” explains Thomas Bürgisser. When the warehouse administration system requests the retrieval of a pallet, the rack servicing crane goes to the pallet position filed in the system, picks up the pallet and transports it to the conveyor system on the apron.
The pallet is then picked up by a crosswise moving carriage and taken to the conveyors. Barcode labels are now automatically put on the goods. The label contains all specifications that guarantee complete tracking of every individual consignment.
“Efficient control of the entire material flow”
The pallet finally gets to one of a total of 26 gravity roller conveyors with a capacity of 17 pallets each. The goods are transported with Jungheinrich electric front stackers to the Goods-out pick-up position and made ready lorry- and tour-specifically for lorry transport.
“SPS control in our warehouse ensures that processes run to precise clock cycles. It allows the warehouse host computer constant monitoring as well as efficient control of the entire material flow”, explains Ulrich Gloor.
Jungheinrich Responsible for Service
There is also high redundancy at the ready in the conveyor system and this ensures availability also for regularly carried out maintenance work. Thomas Bürgisser: “This means that operations were planned by us in such a way that every moving carriage can also take on the work of another one without capacity loss.”
The same also applies to maintenance work on the vertical hoists at Goods-in. “Jungheinrich is responsible for maintaining the entire installation,” adds Gloor. “The service is professional and is carried out reliably and on time, also during weekends.”
Special Safety Gates
Not only identical pallet loads are deposited in the automated high rack warehouse of Lagerhäuser Aarau AG. When an order picking order comes in, the rack servicing crane takes a pallet with the required goods directly to one of the order picking positions dynamically administered by the ERP system.
As the six order picking aisles are directly adjacent to the five RBG aisles, a special safety system was necessary. For excluding theoretical danger to employees, Jungheinrich equipped the interface between RBG and order picking positions with special safety gates: When required, the rack servicing crane automatically opens and then closes the gate again.
“Real added value for our customers”
“We have one gate per pallet position,” recounts Thomas Bürgisser. This means for 1,000 order picking positions also 1,000 safety gates. Ulrich Gloor: “This concept has certainly been a very big plus point against the competition of Jungheinrich.”
In line with the order picking order, the required articles are order picked manually with Jungheinrich electric pedestrian pallet trucks and then made ready for despatch. “The goods can be tracked quickly and completely via the batch number,” explains Gloor. „This is a service with real added value for our customers.”
Order-related RBG performance
Even an automated high rack warehouse does not run for 24 hours and seven days per week at full performance. Jungheinrich offered a special solution to Lagerhäuser Aarau AG for possible under-capacities, for example as occurring in marginal seasons. “When the warehouse has a little less to do, the rack servicing cranes only work at half speed,” says Ulrich Gloor. Instead of the horizontally designed 240 metres per minute, the RBGs then only move at a speed of 120 metres per minute. This applies similarly to vertical movements. A speed of 30 instead of 60 metres per minute is then only available here.
“Jungheinrich integrated different stages here for us to regulate the speed of the rack servicing cranes according to the number of orders in hand,” says Gloor afterwards. This not only had a positive effect on wear and tear but also on maintenance costs. “This Jungheinrich solution also contributes towards saving energy.”
jak – 2010