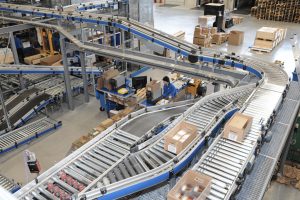
Hilpotstein. The secret to the success of Keller & Kalmbach’s new central warehouse lies in its order picking system. In addition to enhanced process efficiency, a key requirement consisted of ergonomically designed order picking workstations – a job for Jungheinrich, as the general contractor.
There are a number of sights to see driving along the A9 autobahn from Munich to Nuremberg. But when you reach Hilpoltstein there is a real eye catcher – a building complex painted brilliant white, with huge blue letters at the top of the tallest building announcing the name “Keller & Kalmbach”.
Established in Munich in 1878, the company was originally a hardware wholesaler. Today Keller & Kalmbach is one of Germany’s leading wholesalers for fasteners, screws, fastening technology and dowels along with special parts, hand tools, power tools and lifts. The company also manufactures work safety and factory equipment as well as chemical-technical products.
An Investment in Growth and an Investment in Rationalisation
Keller & Kalmbach has its head offices at Unterschleissheim near Munich, currently employs more than 450 people and most recently had annual revenue of more than 150 million euros. The company’s 20,000-plus customers come from the automotive sector, heavy industry and the contracting sector. Keller & Kalmbach maintains a total of 22 branches in Germany.
„The latest milestone in our company’s progress was the construction and commissioning of the new central warehouse for our C parts wholesaling and distribution operations based in Hilpoltstein, to the south of Nuremberg,” says Dr Ingomar Schubert, Head of Supply Chain Management at Keller & Kalmbach. After an 18-month building phase the white warehouse complex located directly on the autobahn was commissioned in summer of 2009. For Schubert, the completion of the new distribution centre was not just an investment in growth, it was also an investment in rationalisation.
Jungheinrich: Planner and General Contractor
For some time the handling capacity at the previous central warehouse – with 9,000 pallet slots and some 60,000 slots for small parts containers – in Unterschleissheim near Munich was no longer able to keep up with the turnover demands at Keller & Kalmbach. Because it was not possible to extend the premises at Unterschleissheim, the nine smaller branch warehouses in southern Germany initially had to cope with burgeoning demand for storage space.
“To meet the surge in growth at Keller & Kalmbach, both qualitatively and quantitatively, it was necessary to build a new, modern distribution centre,” relates Schubert. Jungheinrich was given the go-ahead as the planner and general contractor. “The crucial criterion for winning the contract was that Jungheinrich was a one-stop supplier,” emphasised Schubert. But after-sales service was also a particularly important aspect for Keller & Kalmbach: “After all, our business would not be where it is today without our own professional after-sales service!”
Four Warehouse Sections
The new distribution centre includes four warehouse sections: an automated pallet rack warehouse as an order picking store for large items and as a supply magazine, an automated warehouse for small items stored in cartons and as an order picking store, an automated tray warehouse for storing empty kanban containers and a warehouse for oversized goods. The Jungheinrich Warehouse Management System (WMS) is being used to manage all storage areas.
The well-conceived layout of the warehousing areas means Keller & Kalmbach can react flexibly to future developments and, if necessary, expand storage space. According to Schubert: “This means we can use our new central warehouse flexibly over a very long period of time – even if there are big changes to our business.”
Main Emphasis: Selecting the Right Order Picking System
To achieve extremely high order picking efficiency, special emphasis was placed on the layout of the order picking system when the distribution centre was designed. The concept behind the order picking area was based on the goods-to-man principle. At each of the ten order picking workstations, orders can be picked from different staging units. The relevant conveyor systems from the pallet and the two small parts storage areas run on different levels.
“Thanks to the systems running on different levels, Keller & Kalmbach retains the desired high degree of flexibility with respect to work flows at the order picking workstations,” explains Dr Stefan Seemüller, Head of Automatic Systems in Jungheinrich’s Logistics Systems department.
Six Operations: Highly Flexible Order Picking System at Keller & Kalmbach
- Order picking from warehouse pallet to shipping pallet
- Order picking from small parts container to shipping pallet
- Order picking from small parts container to shipping carton
- Order picking from warehouse pallet to shipping carton
- Filling kanban container with items from warehouse pallet
- Filling kanban container with articles from small parts containers
Goods-to-Man Principle
“We decided to go for an order picking system based on the goods-to-man principle with manual retrieval and decentralised delivery,” remarks Schubert, “in which not only the goods but also the kanban containers are automatically provided.“ According to the logistics expert, the main reasons for this involved the even load throughout the year, the homogenous distribution of the different articles and the high article weights.
Based on these requirements Jungheinrich designed and installed the order picking workstations to allow them to be easily provisioned with diverse staging and shipping units. The ergonomic and technological design of the total of ten multifunctional order picking workstations at Keller & Kalmbach helps the operatives perform the various order picking procedures more efficiently.
High Ergonomic Requirements
“The ergonomic design of the order picking workstations was one of the explicit customer requirements,” recalls Seemüller. For instance, the redundant carrier now only has to be pushed forwards and not to the side – the operative no longer has to twist his body.
In addition, all hand movements are now carried out at an ergonomic height. “This is important, because we depend on manual order picking, which is necessary in view of the great diversity of the articles,” adds Schubert. To ease any doubts Keller & Kalmbach might have had about delivering on the high ergonomic requirements, during the planning phase Jungheinrich set up a demo order picking workstation at its Moosburg facility to be able to highlight practicalities and features to the client.
„We were able to exploit the full rationalisation potential“
Although the level of rationalisation at the combined order picking workstations was already considerable, Keller & Kalmbach were not yet satisfied.
Schubert: “If the operative can now also pick and directly fill the shipping container, the advantage is that the article now only has to be handled twice – once when the articles arrive at incoming goods and twice when the order is being picked. This means we were able to successfully exploit another major rationalisation potential!”
Strengths of the Order Picking System
At Keller & Kalmbach picking orders are bundled into one assignment. The Jungheinrich WMS uses certain criteria for aggregating customer orders received in the HOST system and then sends a pooled assignment to the workstation. “In theory one assignment can contain an infinite number of picking orders,” relates Dr Markus Heinecker, Head of Warehouse Management Systems at Jungheinrich.
According to Heinecker, another highlight of Jungheinrich’s order picking system is the shipping type designation. “Keller & Kalmbach distinguish between different shipping types, including pallet shipping or dispatching small quantities in cartons.” Whereas pallet shipping is handled by a large haulage company, a parcel service is used for shipping small boxed consignments.
Efficient Management of Special Orders
“Jungheinrich’s WMS uses the article weights stored in the master data to calculate the total weight of the picking order and automatically ensure that the right shipping units are provisioned – carton or pallet,” explains Markus Heinecker, adding, “All the information is automatically sent to the relevant transport provider so that the shipping order is placed and executed.”
In addition, the warehouse management system assigns a status to each order picking workstation. Heinecker: “If a picking station is flagged as ,active’, this means all picking orders can be handled.” If the station is assigned ,passive’ status, the WMS can only send certain picking orders – for instance, from a specific customer or high priority orders.
Operatives Involved in Decisions at their Workplaces
Picking stations can also be blocked, for example, if not all ten picking workstations are required. We have integrated this status feature in the order picking system so that the whole system can work flexibly and special orders can be efficiently managed,” sums up Markus Heinecker.
Apart from the ergonomic design of the order picking workstations and the high efficiency of the processes, Keller & Kalmbach also wanted its operatives to be involved in decisions at their workplaces. This was the rationale behind Jungheinrich setting up an interactive order picking interface for carrying out all actions.
Flexible Decision Processes
This is important for organising provisioning. Normally, as soon as the quantity drops below a set minimum threshold for an article in the carton storage system, the WMS automatically issues a provisioning order to the pallet warehouse. An appropriate pallet is then retrieved and delivered to the picking station. Here the goods are then automatically stored singly and in cartons in the small parts storage system.
However, the operative can also decide that provisioning is needed. “This is usually the case,” explains Heinecker, “if the remaining quantity on a pallet is so low after retrieval that it is not worth having the pallet conveyed back to the pallet store.”
Increase Efficiency
“The order picking workstations at Keller & Kalmbach facilitate flexible and efficient working practices,” says Dr Ingomar Schubert by way of conclusion, “as all goods are provisioned and available at the picking station irrespective of the type of container or carrier used to deliver them.”
Schubert continues: “This means you only need concentrate on the tasks which cannot be automated, thus reducing the monotony and enhancing the efficiency of our processes, which in turn makes our staff more motivated and productive.” Similar to when staff members, be they from Keller & Kalmbach or Jungheinrich, see the bright white warehouse complex looming up at the Hilpoltstein exit on the A9 autobahn.
jak – 2010