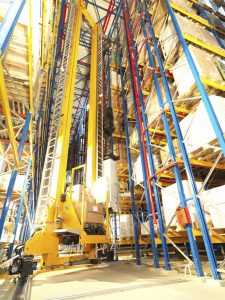
Ruhla. Jungheinrich hat als Generalunternehmer für REV Ritter ein automatisches Hochregallager errichtet. Mit Kreativität und entsprechender Fachkenntnis konnte das Hamburger Unternehmen für den Mittelständler Kosten auch an Stellen einsparen, an denen man zunächst nicht damit gerechnet hatte.
Gero von Randow hat es auf den Punkt gebracht: Technik müsse nicht nur gut funktionieren, sondern vor allem in Welt passen, sprich nahe an den realistischen Gegebenheiten sein. Das Credo des bekannten Wissenschaftsjournalisten hat sich die REV Ritter auf die Fahnen geschrieben. Das Unternehmen mit Sitz im Mömbris bei Aschaffenburg ist eines der führenden Hersteller für Elektro- und Elektroinstallationsmaterial und verzeichnete im Jahr 2008 einen Umsatz von etwa 65 Millionen Euro.
Mit über 300 Mitarbeitern in fünf Werken in Deutschland und Österreich erreichte die Ritter-Gruppe, die sich vor allem auf den europäischen Markt konzentriert, eine Exportquote von 25 Prozent. Neben der Hauptmarke REV hält das Unternehmen seit 2006 die Markenrechte für „Minimax for home“. Unter dieser Marke wird ein hochwertiges Brandschutzsortiment vertrieben.
Erweiterungen am bisherigen Standort unmöglich
Zudem hat REV Ritter im Jahr 2007 ein Joint Venture mit dem Münchner Leuchtmittelhersteller Osram GmbH gegründet und damit ein neues Unternehmen unter dem Namen Ritos in den Markt gebracht. Dieses Gemeinschaftsunternehmen vertreibt funktionale Leuchten für den Endverbraucher. Hierzu zählen insbesondere Beleuchtungen für spezielle Einsatzbereiche wie Küche, Bad oder Hobbykeller. Außerdem wird in Europa der Absatzkanal Retail, also der Selbstbedienungshandel, beliefert.
Zu Beginn der neunziger Jahre stand bei REV Ritter auf Grund deutlich gestiegener Produktionszahlen eine Erweiterung ins Haus. „Da wir am Standort Mömbris jedoch keine Möglichkeiten für eine solche Erweiterung hatten“, erzählt Karlheinz Ritter, Prokurist des Familienunternehmens, „mussten wir uns woanders umschauen.“
So übernahm REV Ritter den ehemaligen VEB Acosta in Thüringen. In den folgenden Jahren wurde das nunmehrige Werk 4 von REV Ritter am Standort Thal (bei Ruhla) Schritt für Schritt aus- und umgebaut, um den Marktgegebenheiten zu entsprechen. „Ungünstige Fertigungsbedingungen durch verschiedene Höhen der insgesamt 18 teilweise sehr kleinen und schlecht zugänglichen Gebäudeteile waren der Anlass hierfür“, so Ritter weiter.
Vorläufiger Höhepunkt war die Errichtung eines vollautomatischen Hochregallagers in Silobauweise. „Auf Grund der Hanglage mussten wir das Lager teilweise bis zu drei Meter in den Boden einlassen“, erläutert Andreas Soika, Projektleiter Logistiksysteme bei Jungheinrich und verantwortlich für den Bau und die Inbetriebnahme des Hochregallagers von REV Ritter.
Vorkommissionierung über Nacht
Im Lager selber können auf sieben Ebenen etwa 6.800 Paletten eingelagert werden. Ein kurvengängiges Regalbediengerät lagert in sechs Gassen ein und aus. In der Nähe der Auslagerstrecke sind zusätzliche Palettenplätze für die Vorkommissionierung über Nacht eingerichtet. „Somit können wir sicherstellen“, erzählt Karheinz Ritter, „dass das Lager am nächsten Morgen sofort auf Hochtouren anlaufen kann.
Das automatische Hochregallager grenzt direkt an das bisherige Lagergebäude, das nun hauptsächlich zur Kommissionierung genutzt wird. Es besitzt drei Etagen. Im Erdgeschoss werden sperrige Güter sowie Display-Artikel für Sonderaktionen von Kunden kommissioniert. Im ersten Obergeschoss erfolgt die Kommissionierung von Kartonware auf Paletten.
Regalbediengerät ohne Fahrantrieb schneller und preiswerter
„Im zweiten Stockwerk werden C-Artikel und Kleinteile aus Fachbodenregalen kommissioniert“, so Ritter weiter. Die unteren beiden Ebenen werden per Fördertechnik direkt aus dem Hochregallager mit Nachschub versorgt. Die drei Geschosse selber sind mit einem Vertikalförderer verbunden. „Hierbei handelt es sich um ein Regalbediengerät ohne Fahrantrieb“, erzählt Soika. „Das ist deutlich schneller und auch preiswerter als ein Lastenaufzug.“
Angelieferte Paletten werden als Wareneingangsavise vom HOST über eine definierte Schnittstelle gemeldet. Diese Meldung beinhaltet alle Informationen über den Artikel und die zu vereinnahmende Menge. Die Menge der Artikel, die auf einer Palette standardmäßig eingelagert werden können, gibt das System vor. „Die Palette ist lagerfähig“, erzählt Ritter, „wenn der Werker ein Etikett mit den entsprechenden Informationen auf eine fest definierte Stelle der Ware geklebt hat.“
Doppelte Prüfung für angelieferte Paletten
Anschließend wird die Palette auf die Fördertechnik aufgesetzt und zunächst komplett geprüft. „Dies geschieht zum Einen durch eine Konturen-, zum Zweiten durch eine Palettenkontrolle“, erzählt Andreas Soika. Hierbei prüfen zwei Klappen zwischen den Rollen den Paletten- bzw. Gabelfreiraum. „Sobald irgend etwas stört“, so Soika weiter, „gibt das System automatisch eine Fehlermeldung.“ Die Palette wird dann direkt über die nächste Spur der Rollenbahn wieder ausgeschleust und muss gerichtet oder ersetzt werden.
Der Produktionsbereich besitzt eine eigene Einlagerstrecke, um Wege, und damit auch Zeit und Kosten zu sparen. Unabhängig davon, über welche Einlagerstrecke die Paletten ins Hochregallager gelangen, werden diese dort vom Regalbediengerät aufgenommen. Die Lagerung der Paletten erfolgt einfach- bzw. doppelttief, wobei bei der doppelttiefen Einlagerung auf Artikelreinheit geachtet werden muss.
Mit Augenmaß und ein paar Ideen preiswerte Lösung realisiert
Das gesamte Regal für das Silolager wurde aus Standardregalmaterial errichtet. Die Verankerung des Regals im Boden wurde komplett durch eine Verdübelung realisiert, was den Eingriff in die Bewehrung der Bodenplatte unnötig machte. Andreas Soika: „Wir haben bewusst eine Konstruktion gewählt, damit die an sich kostenintensive Bodenplatte für Ritter so preiswert wie möglich wird.“
Diese Konstruktion wurde so aufgebaut, dass die äußeren Regalreihen und die Kopfregale die gesamte dynamische Last aufnehmen. Der Kern des Lagers trägt fast nichts. „Mit ein wenig Augenmaß und ein paar Ideen haben wir eine Menge Stahl und somit auch Geld für den Kunden einsparen können“, so Soika weiter, „und haben trotzdem die richtige Steifigkeit und notwendige Dynamik der Konstruktion erreicht.“
Verfügbarkeitsprüfung und Kommissionierung per Dialog
Kundenbestellungen werden ebenfalls vom HOST dem Lagerverwaltungssystem übermittelt. Zunächst wird eine Verfügbarkeitsprüfung angestoßen. Dabei werden auch noch nicht bearbeitete Wareneingangsavisen sowie wenn notwendig Informationen aus der Fertigung berücksichtigt.
Die Kommissionierung in jeder Etage erfolgt beleglos per Datenfunk. Die Mitarbeiter sind mit Handheld-Terminals inklusive Barcode-Scanner ausgestattet, auf denen die einzelnen Positionen der Kommissionieraufträge mit allen notwendigen Informationen – wie zum Beispiel Artikel, benötigte Menge und Adresse des Kommissionierplatzes – angezeigt werden.
Kommissionierer werden wegeoptimiert geführt
„Um unseren Mitarbeitern die Arbeit zu erleichtern und eine effiziente Kommissionierung zu ermöglichen, liegt jeder Artikel immer auf demselben Platz“, erläutert Karlheinz Ritter. „Jeder Kommissionierer wird wegeoptimiert geführt, damit kein Zeitverlust entsteht.“
Durch das Scannen des EAN-Barcodes (Europäische Artikelnummer) und dem Bestätigen der Menge wird jede Entnahme entsprechend verbucht. Ist die Kommissionierung für einen Kundenauftrag abgeschlossen, werden die Paletten gestretcht, mit Versandetiketten versehen und zum Verladen bereitgestellt.
Vertrauen, Akzeptanz und faire Zusammenarbeit
„Überlegungen, an diesem Standort ein Hochregallager mit Kommissionierbereich zu errichten, gab es schon länger“, erzählt Ritter heute. Erste Verbindungen zu Jungheinrich, neben Flurförderzeughersteller auch Generalunternehmer für Logistik-Gesamtanlagen, gab es bereits im Jahr 2002.
Zwei Jahre später erfolgten die Planungen, diese lagen jedoch zunächst wieder in der Schublade. „Eines Tages kam aber ein Anruf von REV Ritter“, berichtet Jungheinrich-Projektleiter Andreas Soika, „mit der Bitte, das damalige Angebot entsprechend zu überarbeiten.
Seriöser und praktikabler Eindruck
Obgleich Jungheinrich preislich im Mittelfeld lag und die Angebote der Mitbewerber von der Leistung in etwa identisch waren, bekam das Hamburger Unternehmen schließlich den Zuschlag. Das Angebot von Jungheinrich habe, so Ritter, einen sehr seriösen und auch praktikablen Eindruck gemacht, was sich in der Realisierungsphase immer wieder bestätigt habe.
„Vertrauen, gegenseitige Akzeptanz und eine faire Zusammenarbeit sind bei solchen komplexen Projekten für uns ganz, ganz wichtig!“ Und auch Gero von Randow hat hier Recht behalten. „Die technische Lösung von Jungheinrich funktioniert nicht nur einwandfrei“, sagt Karlheinz Ritter, „sie passt in unsere Welt und entspricht exakt den realistischen Gegebenheiten!“
jak – 2009