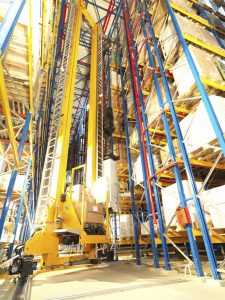
Ruhla. As the general contractor Jungheinrich installed an automated high-bay warehouse for REV Ritter. Using its creativity, ingenuity and wealth of specialist expertise, the Hamburg-based company was able to achieve unanticipated cost savings for the midsize company.
As Gero von Randow, a leading science journalist, put it, technology must not only work well, it must also resolve real world challenges and provide tangible benefits. REV Ritter has made this credo its own. Based in Mömbris near Aschaffenburg, Germany, the firm is a leading manufacturer of electronic products and installation materials, notching up earnings of some 65 million euros in 2008.
With more than 300 employees in five production facilities in Germany and Austria, the Ritter Group, which focuses mainly on the European market, boasts an export rate of 25 percent. In addition to its core brand REV, the company acquired the brand rights to “Minimax for home” in 2006 for marketing a range of high-grade fire protection products.
“We had to look for alternatives”
In 2007 REV Ritter created a joint venture with the Munich-based lighting manufacturer Osram GmbH and launched a new brand on the market under the name Ritos. This joint venture sells functional lamps for the end-consumer, for example for special lighting applications in the kitchen, bathroom or hobby basement. Moreover REV Ritter also supplies retailers in Europe, in particular DIY outlets.
At the start of the nineties, thanks to substantial growth in its production, REV Ritter had to face the challenge of scaling up its activities. “As our location in Mömbris did not offer serious options for expansion,” explains Karlheinz Ritter, General Manager of the family firm, “we had to look for alternatives.”
Installation of a High-Bay Warehouse in Thuringia.
This was how REV Ritter took over the former East German manufacturing facilities of VEB Acosta in Thuringia. To keep pace with market developments, a gradual conversion and expansion of Plant 4 in Thal (near Ruhla) was carried out over the intervening years. “The unfavourable production conditions, for instance the differing heights of the 18 facility buildings, some of them very small and with poor access, made this necessary,” recalls Ritter.
The installation of a fully-automated silo-type high-bay warehouse has been the proudest achievement to date. “Because of the slope we built on, part of the warehouse was recessed up to three metres into the ground,” explains Andreas Soika, Logistics Systems project manager at Jungheinrich and responsible for the construction and commissioning of the high-bay storage for REV Ritter.
Overnight Preparation for Next-Day Order-Picking
Some 6,800 pallets can be stored in the warehouse on seven levels. A high bay warehouse storage and retrieval vehicle with good cornering capability is used for storing and retrieval cycles in the six aisles. Additional pallet areas are used for overnight preparation for next-day order-picking. “This means we can ensure that material handling in the warehouse gets off to a flying start the following morning,” relates Ritter.
The automatic high-bay warehouse is immediately adjacent to the former warehouse — now mainly used for order picking. It has three floors: order picking of bulky goods and display articles for special customer campaigns is done on the ground floor. Order picking palletised goods in cardboard boxes is carried out on the first (upper) floor.
Vehicle Without Traction Drive Faster and Cheaper
“On the second floor C-items and small parts are order picked from shelf racks,” adds Ritter. Conveyors from the high-bay warehouse keep the two lower floor levels provisioned, while a vertical conveyor links all three floors. “We use a high-bay warehouse storage and retrieval vehicle without traction drive,” says Soika. “This makes it much faster and cheaper than a material handling lift.”
The HOST registers all incoming pallets via a defined interface. The notification contains all data on the article and the quantity. The system sets the quantity of articles that can be stored on a pallet. “The pallet is ready for storage once the operative has attached a label with the relevant information to a standardised spot on the article,” says Ritter.
Thorough Check
Then the pallet is placed on the conveyor, where it undergoes a thorough check. “This is done on the basis of a contour and pallet check,” relates Andreas Soika. Two flaps between rollers check pallet and fork space. “As soon as something is amiss,” adds Soika, “the system generates an automatic error message.” The pallet is then automatically taken out of circulation for fixing or replacement.
The production area has its own storage route to save transport distance and hence time and money. Irrespective of the route the pallets take to the high-bay storage, the storage and retrieval vehicle does the rest. The pallets are stored single deep or double deep – only the same articles are permitted for double-deep storing.
Cost-Efficient Solution
The whole racking system based on the silo-design was made from off-the-shelf racking materials. The base of the racking system was secured to the floor with a dowel anchor system to avoid any drastic invasive intervention in the reinforced floor base plate. Andreas Soika: “We consciously selected the most economic structural design to keep Ritter’s costs down in relation to the relatively expensive base plate.”
The structure was designed to ensure that outer racks and the top of the racks are load-bearing. The core of the warehouse almost bears no load. “With common sense and creative ideas we were able to save the customer lots of steel and plenty of money,” Soika adds, “while achieving the proper stiffness and necessary structural integrity of the building.”
Order Picking is Paperless
The HOST also sends customer orders to the warehouse management system. Subsequently, an availability check is performed, which also looks at pending and as yet unprocessed incoming goods notices and, if relevant, information from the production side.
Order picking at all levels is paperless, thanks to wireless technology. Operatives are equipped with handheld terminals with integrated barcode scanners. The terminals show each picking order plus all relevant information, such as the article in question, the quantity, and the order picking address.
“The path each order picker takes is optimised”
“To make things easier for the operatives and ensure more efficient order picking each article is always located in the same place,” explains Karlheinz Ritter. “To save time the path each order picker takes is optimised.”
Scanning the EAN (European Article Number) barcode and confirming the quantity means all retrievals are logged. Once the order picking for a particular customer order has been finished, the pallet is stretch wrapped, a shipping label is attached and it is dropped off at the dispatch area.
Trust, Acceptance and Fair Cooperation
“For some time we had been looking at installing a high-bay racking system with an order picking area,” relates Ritter today. The first contact with Jungheinrich, as manufacturer of industrial trucks and as general contractor for integrated systems, goes back to 2002.
Plans were drawn up two years later, but were initially relegated to the desk drawer. “But one day we got a call from REV Ritter,” recalls Jungheinrich project manager Andreas Soika, “with the request to update the original offer.”
Serious and Practical Impression
Although Jungheinrich’s quotation was average in terms of the price, and the scope of delivery was also similar to the other bidders, the Hamburg-based company got the nod. According to Ritter, Jungheinrich’s offer made a serious impression and was eminently feasible — confirmed time and again during the implementation phase.
“For us trust, mutual acceptance and good cooperation are crucial for the successful conclusion of such a complex project.” Gero von Randow was proved right. “The technical solution put forward by Jungheinrich not only works smoothly,” says Karlheinz Ritter, “it matches our way of doing things and completely takes real world conditions into account.”
jak – 2009