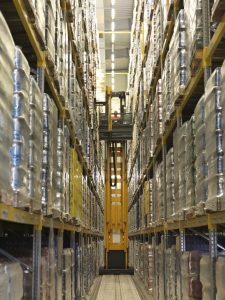
La Valetta. Wenn die Fläche knapp ist, dann muss die Höhe genutzt werden. Das gilt erst recht in kleinen Ländern wie Malta. Nicht nur aus diesem Grund hat sich der dortige Marktführer in Sachen Getränke, die Brauerei Simonds Farsons Cisk plc, beim Bau ihres neuen Warehouses für ein klassisches Schmalganglager entschieden. Für den reibungslosen Ablauf sorgen dort Hochregalstapler aus dem Hause Jungheinrich.
Eigentlich war Malta früher ein Weinland. Erst durch externe Einflüsse, in Hauptsache durch britische Soldaten, fand ein sukzessiver Wandel in Richtung Bier statt. In den frühen Zwanziger Jahren des vergangenen Jahrhunderts errichtete die damalige L. Farrrugia & Sons Ltd. in Hamrun die erste Brauerei auf der kleinen Mittelmeerinsel. 1928 wurde das erste einheimische Bier (Farsons Pale Ale) gebraut, was nicht nur einen Schub für das beginnende Malteser Brauereiwesen, sondern für die gesamte Industrie des Landes brachte.
Im Jahr 1950 wurde eine neue Brauerei errichtet und kontinuierlich modernisiert. Die Produktionsfläche liegt heute bei mehr als 24.000 Quadratmetern. „Für einen langen Zeitraum waren wir nur eine klassische Brauerei“, erzählt Paul Micallef, Chief Operations Officer bei Farsons.
Komplett neue Brauerei in Planung
1952 entwickelte das Unternehmen seinen ersten eigenen Softdrink namens Kinnie und startete mit der Produktion internationaler Softdrinks. Später begann man das erste Malteser Tafelwasser sowie Säfte unter Lizenz herzustellen. Diese Produkte werden heute in ganz Malta, aber in Anrainerstatten wie Italien, Griechenland oder Ägypten, verkauft.
Nachdem im Jahr 1990 ein topmoderner Brauereibereich eingeweiht wurde, konnten 2008 ein neues Warehouse- und Distributionszentrum sowie eine neue Abpackanlage für Softdrinks eröffnet werden. Hierbei handelte es sich um ein Projekt mit einer Investitionssumme von rund 10 Millionen Maltesische Lira (umgerechnet etwa 25 Millionen Euro).
Zahl der Händler reduziert
Mit der Entscheidung für ein eigenes Warehouse- und Distributionszentrum begann Farsons peu a peu auf Händler zu verzichten. „Wir reduzierten die Zahl unserer Händler zunächst von 13 auf acht, dann auf fünf“, erzählt Albert Calleja, Cheif Development Officer. Seit dem Jahr 2008 operiert Farsons nur noch mit einem Exklusivhändler für Gozo – einer sechs Kilometer nordwestlich der Hauptinsel des maltesischen Archipels gelegenen Insel.
Calleja: „Durch die Reduktion der Händler und dem Bau eines eigenen Lagers sind wir in die Lage versetzt worden, unseren gesamten Warehouse- und Distributionsprozess zu kontrollieren. Das hat zur Folge, dass wir unseren ohnehin hohen Qualitätsstandard stetig weiter verbessern können, was im heutigen Marktumfeld überlebenswichtig ist!“
Bei der Errichtung des Lagers galt es, einige Klippen zu umschiffen und Herausforderungen zu meistern. Zum einen ist in Malta Land naturgemäß knapp, das heißt teuer. Da das Unternehmen jedoch im direkten Umfeld der Brauerei in Mriehel Land besaß, wurde beschlossen, das Warehouse- und Distributionszentrum hier zu errichten. „Außerdem hatten wir keine Erfahrung, was beim Bau eines solchen Lagers alles zu beachten ist“, gesteht Paul Micallef. „Hier konnten wir aber auf kompetente externe Partner zurückgreifen.“
Einer von diesen war Jungheinrich. Das in Hamburg ansässige Unternehmen beliefert Malta über den Exklusivhändler Mekanika mit Flurförderzeugen. „Wir kannten Jungheinrich bereits“, erzählt Albert Calleja, Chief Development Officer, „und haben uns mit unserem Anliegen folgerichtig an Mekanika gewandt.“ Im Rahmen dieser Kooperation erfolgte zunächst ein loser Austausch an Ideen, die anschließend direkt in ein mögliches Lagerlayout mündeten. „Von Jungheinrich haben wir auch bezüglich der Spezifikation unseres neuen Warehouses sehr viel hilfreiche Unterstützung erhalten“, so Calleja weiter.
Eine erstmals auf Malta eingesetzte Technologie
„Obgleich in der Getränkebranche Block- beziehungsweise Kanallager üblich sind“, erzählt Thomas Peters, Jungheinrich-Projektingenieur und maßgeblich am Layout des neuen Warehouses von Farsons beteiligt, „spielten zwei wichtige Parameter bei der Projektierung eine besondere Rolle.“
Zum einen wollte und musste Farsons das Lager wegen des fehlenden Platzes und vor allem ob der Hanglage in die Höhe bauen, was ein Blocklager weitgehend ausschloss. Zum zweiten wünschten sich die Betreiber, dass ein direkter Zugriff auf alle Waren möglich sei, was gegen das Kanallager sprach. So entschied man sich gemeinsam mit Jungheinrich für den Bau eines Schmalganglagers.
Lager-Layout von Jungheinrich
„Wir hatten schon ein wenig Angst davor“, bekennt Albert Calleja heute lächelnd. Erstes handelte es sich hierbei um eine auf Malta noch nie eingesetzte Technologie „inklusive des Betriebes von Hochregalstapler“. Zweites habe man gespürt, dass die Bereitschaft der Mitarbeiter, mit einem Hochregalstapler zukünftig auch in Höhen bis zu 15 Metern zu arbeiten, „zunächst nicht besonders ausgeprägt war“, so Calleja. „Wir haben in der Tat ernsthaft den Einsatz von Man-Down-Geräten geprüft.“
„Die ‚Angst’ vor dem Schmalganglager konnten wir sehr schnell beseitigen“, erinnert sich Peters heute noch. Man habe sich gemeinsam sehr intensiv mit diesem Thema befasst, „und auch schon relativ früh alle notwendigen Details besprochen“. Nachdem Jungheinrich das Layout für das komplette Lager beigesteuert hatte, wurde das Hamburger Unternehmen schließlich mit der Lieferung der Schmalgangfahrzeuge sowie der Legung der Induktivführung beauftragt.
11.000 Paletten auf 5.000 Quadratmetern
Das neu errichtete Warehouse- und Distributionszentrum von Farsons ist etwa 5.000 Quadratmeter groß und kann mehr als 11.000 Paletten beherbergen. Neben einem kleineren Bereich, in dem bei einer konstanten Temperatur von 15 Grad Celsius exquisite Weine und Spirituosen gelagert werden, erfolgt die Lagerung der am Standort produzierten Biere und Softgetränke in einem geteilten Bulk-Lager.
„Der Bereich, in dem das Bier gelagert wird, besitzt eine Temperatur von konstant 21 Grad Celsius“, erläutert Christopher Borg Cardona, Distribution Manager bei Farsons (Sales & Marketing) Ltd. „Außerdem muss das Licht in diesem Bereich entsprechend gefiltert werden, da ultraviolette Strahlen die Qualität des Bieres, das in helle Flaschen abgefüllt worden ist, beeinträchtigen kann.“
Damit die Ein- und Auslagerprozesse effizient von Statten gehen, setzt Farsons auf Schmalgangstapler von Jungheinrich. Während im Wein- und Spirituosenlager ein Kommissionier- und Dreiseitenstapler vom Typ EKX 410 seinen Mann steht, sorgen drei Fahrzeuge der Baureihe 5, die im Jahr 2007 in den Markt eingeführt wurden, für Hochleistungen in Farsons Bulk-Lager.
Bei den hier eingesetzten Geräten handelt es sich um den Typ EKX 515 mit einer Tragkraft von bis zu 1.500 Kilogramm. „Diese Fahrzeuge erreichen spielend Hubhöhen von 15 Metern“, erläutert Gilbert Debono, Sales Manager Industrial Products beim Jungheinrich-Händler Mekanika. „Dank der 80-Volt-Drehstromtechnik sind diese Fahrzeuge besonders leistungsfähig, was insbesondere in der Getränkebranche immens wichtig ist.“
„Der Mensch stand im Mittelpunkt“
Bei der Entwicklung des EKX 515, der auch Kombistapler genannt wird, da der Bediener mit diesem Gerät sowohl stapeln als auch kommissionieren kann, habe der Mensch im Mittelpunkt gestanden, erzählt Christian Lammek, Händlerbetreuer Südost-Europa für Jungheinrich.
„Der Staplerfahrer kann die geräumige Kabine über einen großzügig dimensionierten Einstieg erreichen. Zudem bietet sich ihm durch die sehr niedrige Schwenkschubführung und die Freihubgerüste eine hervorragende Sicht auf Fahrbahn und Last.“ Für das Wohlbefinden des Fahrers sorge darüber hinaus ein gefederter, verstell- und klappbarer Komfortsitz, der auf Wunsch mit Heizung und Lendenwirbelstütze ausgestattet werden kann.
Deutliches Mehr an Komfort und Sicherheit
Ein deutliches Mehr an Komfort und Sicherheit des EKX 515 im Vergleich zu anderen Fahrzeugen hat auch Christopher Borg Cardona festgestellt. Hierzu zählt unter anderem ein schalterloses Zweihand-Bedienkonzept. Im Mittelpunkt des Arbeitsplatzes am Stapler steht das elektrisch verstellbare Bedienpult. Es bietet als zentrale Steuerungs- und Informationseinheit eine Vielzahl innovativer Leistungsmerkmale und besitzt ein Farbdisplay sowie eine Folientastatur mit Ziffernblock.
„Über einen Zugangscode kann der Bediener individuell angepasste Fahrerprogramme abrufen“, ergänzt Debono. Die schalterlosen Sensoren registrieren die Berührung durch den Bediener und geben diese Informationen an den Bordrechner weiter.
„Jungheinrich war immer sofort zur Stelle“
„Die Fahr- und Hydrauliksteuerung selbst wird mit der bewährten Daumenbetätigung gesteuert“, so Lammek. Dass die Warehouse- und Distributionsprozesse bei Farsons auch in Zukunft auf einem sehr hohen Qualitätsstandard laufen, hat – darin sind sich alle am Projekt beteiligten Personen einig – gerade mit dem Einsatz der hoch technologisierten Kombistapler von Jungheinrich zu tun.
„Auch wenn es“, ergänzt Albert Calleja lächelnd, „die bei einem solch’ komplexen Projekt beinahe üblichen Anfangsschwierigkeiten auch gegeben hat.“ Jungheinrich sei, so der Manager weiter, aber immer und sofort zur Stelle gewesen, wenn es bei der Softwareimplementierung anfangs auch mal gehakt habe.
Techniker stehen jederzeit auf Abruf bereit
Nicht nur für diesen Zweck hat Jungheinrich eigens Techniker auf Abruf, die notfalls innerhalb von 48 Stunden an nahezu jedem Ort der Welt zur Stelle sein können. Einer dieser Techniker ist Rudolf Kornbauer. Der im bayerischen Moosburg, am Produktionsstandort des EKX 515, ansässige Experte, hat bei der Überwindung von anfänglichen Implementierungsschwierigkeiten nicht nur die eigenen Kollegen, sondern insbesondere die Zuständigen bei Farsons begeistert
Albert Calleja: „Wir waren überrascht, wie exakt ein Mensch die Komplexität dieser Fahrzeuge beherrschen kann!“ Diese Begeisterung hält auch heute noch an: Farsons hat mittlerweile einen weiteren Kommissionier- und Dreiseitenstapler vom Typ EKX 515 von Jungheinrich erworben.
jak – 2010