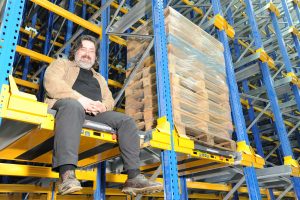
Moscow. In the south of Moscow lies a compact warehouse where imported frozen meat is transhipped. Recently equipped with a shuttle system, the storage facility makes ideal use of space. For warehouse operator Universal Services, its long-standing professional cooperation with Jungheinrich was pivotal to awarding the contract.
Speaking to Michail Lyubovich, it becomes immediately apparent that the Moscow-based entrepreneur is proud of what has been created here in the south of the Russian metropolis. The main grounds of the former state railway company are located half way between the city centre and Moscow Domodedovo Airport. Until well into the 1980s, railway carriages were still being produced here for the former Soviet Union.
The beginning of Perestroika saw the start of the complete conversion of the whole complex. Railway carriage production was relegated to the past. What remained were the administrative building and a few halls. In 1996 Universal Services – a company offering a wide range of logistics services, including refrigeration logistics – bought the land.
Newly Built Refrigerated Warehouse
In cooperation with a German logistics company, it quickly installed and opened a refrigerated warehouse in the still extant buildings. With success: “After the financial crisis in Russia at the end of the nineties, Universal Services was practically the only surviving logistics provider with experience in operating refrigerated warehouses,” says Michail Lyubovich, owner of Universal Services in Moscow.
Today Universal Services continues to operate successfully as a logistics service provider in Russia. The latest example: A newly built refrigerated warehouse on the old railway grounds. The company’s new complex provides logistics services to the meat wholesale trade in Russia, handling imports mainly from Europe, USA, Mexico, South America and increasingly Australia.
Handling Polyblock Pallets a Challenge
The frozen meat handled at this facility is delivered for refrigeration in the form of polyblocks on pallets. “Handling polyblock pallets is a huge challenge,” explains Lyubovich. “A standard rack designed for three pallets has room for just two polyblock pallets.”
On the other hand block storage won’t work either, because a maximum of just two polyblock pallets can be stacked on top of each other. “For this reason we decided to build a special refrigerated warehouse for polyblock pallets.”
Compact Channel Storage Systems with Shuttles
To maximise the use of space, Universal Services considered installing compact channel storage systems with shuttles in the new refrigerated warehouse. The range of services of a traditional compact storage system, which saves space by doing away with aisles, are augmented by shuttle systems, as they open the potential for optimising the fill level, throughput rate, article diversity and volumetric efficiency in addition to enhancing cargo handling protection.
Shuttle systems for their part allow the efficient storage of palletised goods and commodities in compact channel storage systems. At Universal Services in Moscow pallets, each weighing 1,300 kilogrammes, can be stored in over 9,000 slots. Depending on the type of pallet – Euro-pallet or CHEP pallet – the channel can take on 27 or 20 pallets, respectively. A total of six Under Pallet Carriers and two ETV 320 reach trucks ensure smooth and synchronised logistics operations inside Universal Services’ refrigerated warehouse.
Cooperation for Some Ten Years
As early as 2006, Michail Lyubovich had already seen such shuttle systems in action – albeit on video – at an industrial fair in Moscow. With this memory in mind ,the owner of Universal Services approached Jungheinrich, which had already been successfully cooperating with Universal Services for some ten years.
“In the end, our many years of positive experience with Jungheinrich was the decisive factor for awarding this crucial contract to Jungheinrich,” says the proprietor of the Moscow-based logistics company. Absolute satisfaction with the quality and level of service provided by the Hamburg-based intralogistics specialist shored up the deal. “We can’t afford to experiment!” he exclaims.
Storage Errors Virtually Eliminated
There’s no experimenting either when it comes to material flows. Incoming goods are palletised, checked, weighed, then scanned to log them automatically in the warehouse management system (WMS). The WMS assigns the storage location. A gravity conveyor takes the pallet from incoming goods to the refrigerated storage. There a stacker operator scans the pallet and the WMS immediately issues the instructions via the operator’s terminal to drive to a particular channel.
An RFID tag is fitted to each channel in Universal Services’ compact refrigerated warehouse. The WMS checks that the channel is the right one and that a shuttle is ready. If the OK signal is returned, the pallet is set down on the shuttle, and the shuttle takes care of storing the pallet automatically. In Lyubovich’s words, “Storage errors are practically ruled out.”
Use of Under Pallet Carriers
As the warehouse system at Universal Services is fitted with longer channels, it quickly became clear that Under Pallet Carriers (UPCs) from Jungheinrich would be the best solution. This kind of shuttle moves under the pallet and then takes up the unit load on its carrier platform.
“The way in which a UPC works is simplicity itself,” explains Alexej Vershynin, Head of Systems, at Jungheinrich in Russia and responsible for the project at Universal Services. “One of the reach trucks picks up the UPC on its forks and places it in the relevant pallet channel.”
Independent Control of All Travel and Lifting Actions
In the channel, the carrier moves independently under the pallet. There is no physical link between the truck and the carrier. So once the truck positions the UPC in the racking channel and the operator pushes the start button on the control terminal inside the reach truck, the onboard control in the shuttle takes over independent control of all travel and lifting actions.
Sensors recognise the positions of the stored pallets. The storage of new pallets and retrieval of stored pallets occurs without any collisions. While the shuttle is moving up and down the channel the reach truck driver is free to pick up another pallet for storing and place it at the start of the channel. This is the beginning of a new storage operation. The retrieval of pallets is similar, more or less in reverse.
Shuttle Automatically Moves Pallets to Front of Channel
For goods dispatch, the driver in the reach truck receives an order and instructions from the WMS. While he drives to the channel indicated, “the shuttle automatically positions pallets at the head of the retrieval end of the channel,” explains Vershynin.
In the case of completely clearing a channel, which frequently occurs at Universal Services because a channel full of pallets is roughly one load for a haulage truck, the UPC automatically moves each pallet to the retrieval end of channel storage.
Efficient and Smooth Material Flows
Here the operator picks up the individual pallets and drops them off at the gravity conveyor for transport to outgoing goods. This is where they are prepared for shipping and delivered deep-frozen by haulage truck to the meat wholesalers.
Michael Lyubovich can justifiably be proud not only of the new, space-saving refrigerated warehouse in south Moscow, but also of the efficient and smooth material flows achieved with the Jungheinrich shuttle systems.
jak – 2012